
Production safety
Due to objective factors, the Group’s activities involve production processes of increased danger. The equipment used is complex and the processes often use high temperature and pressure. In order to ensure a safe working environment, special methods and technology must be applied.
VKG carries out systemic work in the area of production safety. A clear, understandable and fulfillable system of safety rules has been established. Our employees and subcontractors have the right to refrain and/or refuse from fulfilling work tasks which may damage human health or the environment.
2019 in figures
In 2019, the Group registered a total of 17 work accidents, which is one more than in the preceding year. No fatal work accidents took place with the Group’s employees. Unfortunately, a work accident with an employee of a subcontractor ended fatally.
We are working towards preventing and avoiding accidents. If an accident does happen, an inquest is held and measures are taken to minimise the probability of similar accidents in the future. Prophylactic measures are applied in accordance with a plan in all the subsidiaries of the Group.
In 2019, four work accidents that ended in serious injury and eleven work accidents with light injury happened and in two work accidents only first aid was needed. Compared to 2018, the number of serious work accidents dropped by three cases, while the number of light work accidents grew by four.
Serious accidents took place in the following subsidiaries:
- VKG Kaevandused – 4
In 2019, the main reasons for accidents at work were the following:
- violation of occupational safety requirements by an employee;
- nonconformance of pathways/workspace to safety requirements;
- ignoring the use of individual means of protection;
- insufficient arrangement of work.
THE NUMBER OF ACCIDENTS AT WORK BY YEARS WITH THE INDICATION OF THE NUMBER OF EMPLOYEES
- Minor accidents
- Severe accidents
- Number of employees
THE NUMBER OF ACCIDENTS AT WORK PER EMPLOYEE IN 2009-2019
2015 | 2016 | 2017 | 2018 | 2019 | ||
---|---|---|---|---|---|---|
Number of employees | 1995 | 1785 | 1776 | 1761 | 1746 | |
Number of accidents | 14 | 26 | 19 | 16 | 17 | |
Number of accidents per employee | 0,007 | 0,015 | 0,011 | 0,009 | 0,010 |
In total, in 2009-2019 the largest number of accidents (both serious and minor ones, including those requiring first aid) took place at VKG Oil, i.e. 57, while 35 accidents took place in VKG Kaevandused and 32 accidents took place in Viru RMT. A great number of accidents at a workplace in the companies mentioned above is due to a high level of danger of the works performed at them (underground mining, handling hazardous chemicals, repair and servicing of technological equipment) as well as the number of employees.
The most important measures aimed at improving the working environment in 2020:
- upgrading the system of registering dangerous situations,
- an in-depth analysis of the causes of work accidents and emergencies occurring in the Group, and review of prevention measures,
- increasing the awareness of employees and subcontractors and promoting safety culture,
- organising occupational safety training and exams by means of an online learning environment in all the enterprises,
- preparation of video instructions,
- improvement of communication;
- meeting with the representatives of contractors.
Below, we present the total recordable incident rate, or the statistics pertaining to the TRIR indicator for the past three years, which represents the number of accidents at a workplace per one million working hours. The average TRIR-indicator in the Group has been in the downward trend: it has dropped by 20% in the past three years.
2017-2019 TRIR AVERAGE FIGURES
2017 | 2018 | 2019 | ||
---|---|---|---|---|
Viru RMT | 12,0 | 11,2 | 6,1 | |
VKG OIL | 6,4 | 5,7 | 3,3 | |
VKG Energia | 0 | 9,6 | 14,9 | |
VKG Logistika | 9,1 | 0 | 8,9 | |
VKG Elektrivõrgud | 0 | 0 | 0 | |
VKG Kaevandused | 5,2 | 4,2 | 6,6 | |
VKG Soojus | 0 | 0 | 0 | |
Average in the Group | 6,0 | 5,2 | 4,8 |
Working environment under close carel
The main objectives of people engaged in occupation safety matters are to support and keep occupational safety requirements in constant focus and contribute to the development of the working environment by making it safer and more attractive.
Working environment specialists act as the consciousness of our smooth and safe production processes. In total, there are 10 working environment specialists who handle working environment issues in the Group. Every subsidiary has one such specialist and our largest subsidiary, VKG Oil, has three. The work of the working environment specialists is curated by the Safety and Quality Manager.
The Group has implemented a system of working environment representatives: more than 60 representatives of the employees have been elected in the entire Group. All the employees can run for the position of a working environment representative and thereby participate in the work of the Working Environment Council. The engagement of employees in discussions and workshops related to work safety is our ordinary everyday practice. Working environment representatives are those who “carry the voice of the people” and are tasked with noticing and registering and thus improving the working environment. Working environment representatives actively and closely cooperate with working environment specialists and are included in various workgroups. For instance, we organise joint visits for working environment specialists and representatives to other companies in order to learn their functioning and successful practices. The working environment representatives of our subsidiaries meet regularly, with the frequency of the meetings established individually in each enterprise. Once a year, the general meeting of all the working environment representatives takes place, convened by the Safety and Quality Manager.
Work with subcontractors
Viru Keemia Grupp makes efforts to engage subcontractors into focusing on occupational safety matters. All the contracts contain requirements for compliance with general production safety standards and rules as well as internal production safety, occupational and environmental safety rules. In work processes, work environment specialists monitor the conformity of activities with safety requirements and the safety-related details of contractors. In the case of deviations, cooperation is performed in accordance with their decision.
Safety culture
Responsibility and constant development form the basis of safety culture. In order to shape the safety culture, a training system based on legal requirements, corporate standards and international practices has been created.
We acknowledge the decisive role of employees in maintaining a safe working environment and we therefore pay special attention to a dialogue with employees. We organise safety days where employees and subcontractors discuss the risks arising in the performance of works and in which the Group’s top-level managers also participate. This allows us to receive high-quality feedback and ensure the operative elimination of difficulties arising at workplaces.
Children’s drawing competition ‘Work Safety Is IN’
From the beginning of April until the end of May, we held a children’s drawing competition dedicated to work safety, ‘Work Safety Is IN’. The competition received a total of 58 great, contemplated, interesting and heartfelt works: 10 in the older age group and 48 in the younger age group. Young artists from the schools of Kohtla-Järve, Jõhvi, Illuka and Narva had put their vision of the topic on paper.
The aim of the drawing competition was to draw attention to the need to comply with work safety requirements and to the role of work safety, share work safety related information to parents through school children, and demonstrate the children’s understanding of how compliance with work safety requirements helps save human lives.

Internal photo and video competition ‘Work Safety First!’
From the beginning of April until the middle of May, we held an internal photo and video competition dedicated to work safety, ‘Work Safety First!’. The largest number of works were on the topic ‘STOP dangerous work techniques or STOP it-will-never-happen-to-me situations!’.
The best video work of the competition was Sergei Shkadov’s video ‘Work Safety Means Life’. His work vividly presented the correct attitude towards a colleague who does not perform work tasks safely. When an employee tries to fulfil a work task without using personal protection equipment against falling, a colleague stops him and points out the use of correct protection equipment.

The best photo work was Sergei Kirbenyov’s photo duo titled ‘Work Safely, Work Smartly’. He conveyed the meaning of his work with two photos: the first photo showed how one must not work and the other showed the correct way of working. Side by side, these photos demonstrate the vast difference between working with or without personal protection equipment.
Use of IT solutions in production safety
The introduction of information technology in the area of production safety is essential for high-quality results. In the current stage, we are implementing various projects of introducing digital methods for analysing the production safety situation and the management of risks. We want to introduce the developed solutions as an integral set, involving as many employees of the Group as possible.
For instance, platform ‘Give Notice of Risks!’ for gathering information from employees and contractors concerning dangerous activities and conditions in the territory and on the sites allows us to promptly notify the responsible persons and to take measures to exclude violations.
The automation of processes reduces the response time and excludes the probability of loss of important information. The platform gathers a large amount of data on the spot. An analysis of the initial data allows us to identify areas which are problematic from the viewpoint of production safety and require a systemic approach.
Another area which we are focused on is related to transferring the training on production safety rules and conduct in critical situations to the electronic environment and, in the future, also to the virtual reality environment.
Preparedness for the elimination of emergency situations
The Group has developed and implemented a functioning set of measures aimed at the prevention and elimination of emergency situations in the industrial enterprises of the Group. The system ensures:
- the planning and implementation of measures to prevent emergency situations;
- the protection of employees and production facilities;
- an increased reliability of the functioning of production facilities;
- a decrease in the risk of occurrence of emergency situations of technical origin;
- the minimisation of proprietary damage in the case of emergency situations;
- the elimination of the consequences of emergency situations caused by natural and technological factors in accordance with the respective action plans.
The Group has established a plan of regular exercises and training sessions. In exercises, the employees practice the following practical activities:
- reporting the occurrence of an emergency situation;
- bringing the accident and rescue unit into readiness for action;
- fault-free stoppage of technological equipment;
- localisation of accidents;
- using individual protection equipment and primary firefighting equipment;
- helping casualties.
VKG earned the Smart Industrialist Award
The Estonian Association of Engineers and Enterprise Estonia recognised the most innovative industrial enterprises that have set a good example in the area of digitalisation and automation in 2019 with the Smart Industrialist Award.
By today, a fourth of the Estonian industrial sector on the average has engaged in the digitisation of its production processes in the extent of at least 40%, and the consistent and constant application of digital solutions in industry will ensure Estonia’s success in global competition.
Viru Keemia Grupp received the award in the category of large enterprises, because it had interfaced various automatic systems and improved the efficiency of business processes over the past year. The Smart Industrialist Award is intended for recognising enterprises that have contributed to the growth of the added value and productivity of the Estonian economy, thereby contributing to the growth of the competitiveness of the whole of Estonia.
Watch our introductory video here:
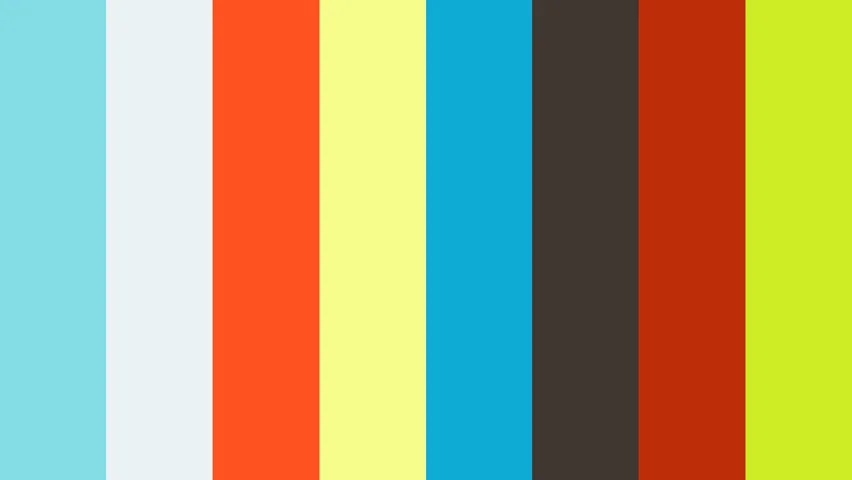